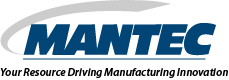
According to MANTEC's LEAN Manufacturing process, there are 8 categories of waste that you should be monitoring:
The benefits of LEAN manufacturing range from the tangible improvements to intangible benefits as well
There are a number of both tangible and intangible benefits of using LEAN tools to improve your business. Tangible benefits include: reduced lead time for orders, reduced costs, improved quality, inventory reductions, increased productivity, and work space utilization. Some of the intangible benefits include: improved employee morale, better teamwork, improved customer perception, and increased brand awareness.
LEAN Manufacturing Stages
The LEAN Manufacturing process consists of 3 key stages that businesses should focus on:
- Identify your waste – Wasteful processes exist across all businesses and all industries. No matter how good you think your processes are right now, they can always be better. Take a close look at how materials and processes flow through your organization to bring products / services to your customer. Identify non-value adding activities and move to stage 2.
- Analyze the waste and find the root cause – Figure out what is causing your identified wasteful activates and begin stage 3. Don’t just put a Band-Aid on the problem; find the problem’s root cause by brainstorming and cause & effect techniques.
- Solve the root cause and repeat the cycle – Decide what actions you must take to fix the issue and create a more efficient process. Commit to continuous improvement and repeat the cycle to fix issues and add value.
LEAN Manufacturing can greatly benefit your organization; contact C.H. Reed and we can point you in the right direction.
C.H. Reed partners with MANTEC, a Pennsylvania based non-profit organization dedicated to meeting the needs of small to mid-sized manufacturing enterprises who are willing to commit to improvement.