April 21, 2021
Guide to Rotary Screw Air Compressors
SHARE THIS POST
The purpose of rotary screw air compressors is to provide an efficient and reliable compressed air source used for various tasks throughout industrial and manufacturing plants. These compressors produce compressed air by utilizing a unique system for trapping the air between two meshed rotors, which can offer some benefits over other types of air compressors. Check out the following rotary screw air compressor overview to learn more about what these compressors are, how they operate, and how companies use them all over the world.
What Are Rotary Screw Air Compressors?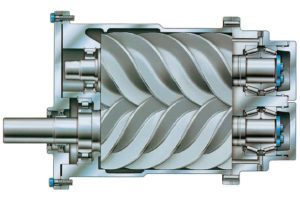
Rotary screw air compressors are an advanced type of air compressor designed to trap air in a compression chamber, between a couple of meshed rotors. The male and female rotors spin, reducing the trapped air’s volume and discharging it from the air end to create compressed air. This air is then fed to workstations throughout a manufacturing plant and is used for a wide variety of different tasks; from inflating tires to operating different types of pneumatic tools, equipment, and conveyors, to even spray painting cars, parts, or machinery.
How Do Rotary Screw Air Compressors Work?
If you want to know more about the mechanics of a rotary screw air compressor, start at the twin rotors. as stated above, these feature female and male parts that rotate oppositely. As these rotors move, the air is trapped in the space between the rotors. The rotors then decrease the surrounding volume between the two and compress air into a smaller location.
A rotary screw air compressor’s pressure ratio changes based on its discharge port’s form, the screw’s pitch and the screw’s length. These compressors don’t require any other mechanical components or valves to work appropriately. As a result, rotary screw air compressors are protected from unbalance. This allows the compressor to operate at high speeds and have a large flow rate.
What Are Rotary Screw Air Compressors Used For?
Companies often use rotary-screw compressors to generate compressed air for all types of industrial applications. Typically, when equipment and machinery need constant compressed air to perform a task, rotary screw air compressors are the best choice. Other types of air compressors, like reciprocating air compressors, generate a lot of heat and need to cycle off more often to maintain the lifecycle of the machinery. Rotary screw air compressors can run continuously and experience little to no downtime, making them the ideal choice for high-production manufacturing applications. You can find examples of their use in automated manufacturing systems, food packaging plants, furniture manufacturing, automobile manufacturing industries, plastics & rubber product manufacturing, metal product manufacturing, commercial printing, woodworking, and much more.
Types of Rotary Screw Air Compressors
Rotary screw air compressors often fall into two categories — oil-lubricated and oil-free. Find out more about these two types to help you pick the right one for your needs:
Oil-Free
An oil-free rotary screw air compressor features external gears tasked with synchronizing the positions of the counter-rotating screw ends. Since these screw ends don’t contact each other, no friction occurs, removing the need for lubrication. They also have non-contacting carbon ring seals that aid their cooling, preventing any chance that oil may enter the air stream inside the compressor. Typically, oil-free rotary compressors are used in applications where no oil should ever enter the airflow, such as for medical oxygen, food packaging, chemical, or electronic product manufacturing.
Oil-Lubricated
Oil-lubricated rotary screw air compressors rely on oil to lubricate and cool compressor air-ends and reduce leakage during discharge. In this compressor, oil is injected into its compression chamber. After the oil lubricates and cools key components, the compressor separates the oil and sends it through a filter before it repeats the process. Companies often utilize these compressors to create high pounds per square inch (PSI) and cubic feet per minute (CFM) on a constant basis.
What Parts Make up a Rotary Screw Air Compressor?
Rotary screw air compressors are made up of a few parts. This type of compressor features:
- Rotors
- Compression cylinder
- Oil filters
- Air filters
- Bearings
- Inlet Valve
- Motor
- System control
- Separators
- Seals
- Gaskets
- Storage tank
One of the most important parts of a rotary screw air compressor is its rotors, as they’re responsible for drawing in air for compression.
Rotary Screw Air Compressor Benefits
Rotary screw compressors offer some distinct advantages over reciprocating compressors, especially when continuous compressed air is needed:
- Flexibility & Adaptability: Every manufacturing facility is different, whether it’s the location or climate they are in, or the different products they are making. Variable speed rotary screw compressors offer the ability to adjust the speeds at which the screws turn, depending on the company’s needs and production shifts. They can also be cooled efficiently, meaning they’ll operate properly in both higher temps and humidity levels. Simply put, they can run in continuous duty, all day, and in all extreme weather conditions without wearing out critical components.They are also flexible in their control operations and capabilities. Advanced controlling technologies offer more insight into your compressed air production than ever before. Our Controls Department can help you install control solutions where you’ll be able to remotely monitor your system, custom program your system to your specific needs, and collect data for continuous improvement in your system. We can even help you network different brands of air compressors together, to give you a central controller. The network will give you the ability to automatically start, stop, load, and unload the units as demand fluctuates – providing optimal energy efficiencies.
- Increased Energy Efficiencies: Rotary screw air compressors form an air-tight seal between their internal rotating screws, which is highly efficient in drawing in and forcing air through the intake. Since 76% of an air compressor’s total life cycle cost comes from electricity used to power the machine, it’s extremely important to choose an energy-efficient unit to give you the most powerful return on investment. (There are many other factors that go into creating an energy-efficient system, which can be found in our blog here.)
- Safe, Convenient, Quiet Operation: Rotary screw compressors are extremely safe. You hardly ever hear about accidents with these machines. They are convenient in the fact that deliver air continuously, without interruption, and can easily be stored anywhere in the plant due to their small footprint. Lastly, despite being able to deliver massive air flows, these machines are generally quiet, with many having advanced noise dampening technologies built-in.
- Easier to Maintain: Rotary screw compressors have fewer rotating parts compared to reciprocating compressors. This in turn lowers maintenance costs. However, although rotaries are easier to maintain, they still require routine, planned maintenance schedules to reward you with many years of productivity and reliability. They also require more skilled maintenance professionals to properly inspect, maintain, and repair them. Check out our customizable preventative maintenance programs for more info.
Though there are many rotary screw air compressor advantages, you should be aware that these units typically hold a higher upfront purchase price compared to reciprocating compressors. If you’re in the market for a new rotary screw compressed air system, perhaps the most important thing to keep in mind and understand is the difference between price vs. cost. That is the upfront purchase price vs. the total life cycle cost of the machine. The majority of the unit’s cost isn’t in the purchase price, but in the electricity required to operate the machine over time.
- Purchase price = 12% of total lifecycle cost
- Maintenance = 12% of total lifecycle cost
- Electricity = 76% of total lifecycle cost
This is why rotary screw compressors are actually less costly to own and operate compared to less energy-efficient reciprocating compressors, despite having a higher upfront purchase price.
Rotary Screw Air Compressor Maintenance
As previously stated, getting your rotary screw compressor on a routine, scheduled maintenance program is crucial to ensuring a long, reliable life. Some of the critical maintenance practices that our factory-trained service technicians perform on your compressed air system include:
- Airend Inspections
- Drivetrain Inspections
- Motor Lubrication Checks
- Lubricant (Oil) Checks
- Filter Changes
Implementing a preventative maintenance schedule for your rotary screw compressor with C.H. Reed will absolutely minimize compressor downtime, minimize costly emergency repairs, lower your energy costs, prolong equipment life, lower your total cost of ownership, and provide you peace of mind knowing your system is running smoothly and saving you money in the long-run.
Choose C.H. Reed for Your Rotary Screw Air Compressor Needs
If you’re located in the mid-Atlantic region, including Pennsylvania, Maryland, Delaware, Virginia, West Virginia, Ohio, and Southern New York, and are interested in learning more about rotary screw air compressors, turn to C.H. Reed for your equipment and maintenance needs. We’re proud to partner with top-tier brands, like Quincy Compressor and Chicago Pneumatic, who are known for their exceptional reliability and wide range of horsepower options. With over 70 years of experience and a team of expert staff, we’re ready to help you find the best rotary screw air compressor for your specific needs.
To start the conversation, contact us today.
Search
Categories
Get a consultation
Related Posts
The 3 Distinct Advantages of Hydraulic Powered Pumps
Recently, C. H. Reed helped a major printing operation install a new ink pumping system. The new system needed to transfer four colors of high viscosity, heat-set ink to their three presses, drawing the ink from multiple 5,000…
Simple Ways to Reduce Waste in Your Spray Finishing System
In today’s demanding manufacturing landscape, it can be convenient to adopt a “cut-costs-at-all-costs” mentality, justifying questionable means for the sake of leaner production, a lower bottom line and increased profitability. Regrettably, those efforts can interfere…
What You Need to Know About Air-Powered Pressure Washers
Pressure washers are great solutions for your average cleaning applications, but what tool do you turn to for your more challenging applications? There are many instances where it is simply impossible to use a traditional…