March 23, 2022
C.H. Reed Helps Crane Manufacturer Win Kaizen Award & Save $150k+
SHARE THIS POST
Grove by Manitowoc
Since 1947, Grove by Manitowoc has been one of the world’s leading producers of mobile hydraulic cranes. Their well-earned reputation for quality and reliability remains unmatched in their industry.
Grove and C.H. Reed have a business relationship that dates all the way back to the late 1940s, which was started by John L. Grove himself and Harold Reed of C.H. Reed. Throughout the years, C.H. Reed and Grove have maintained that relationship with a partnership approach as we work together to help them find and identify value-added solutions that help enhance their compressed air, paint finishing, and fluid handling processes and equipment.
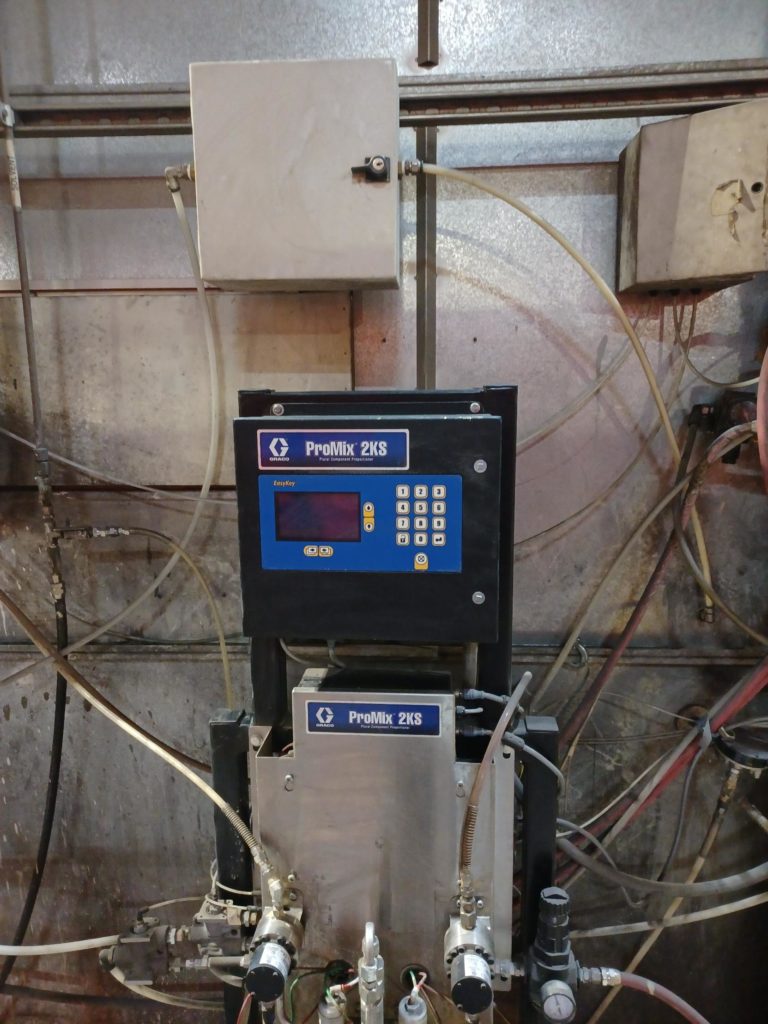
Air Operated Lock Boxes
Americas Lessons Learned Kaizen Award
In early 2021, Grove was presented first place for the Americas Lessons Learned Award, an internal Kaizen award presented by the Manitowoc Company. Later in the year, all first-place submissions were then reviewed by Manitowoc facilities on a global platform, in which Grove won first runner up for the project.
The Project
The project that C.H. Reed worked on with Grove was recognized for the following reasons:
- Increased Energy Efficiency
- Waste Reductions
- Emissions Reduction
- Quality
We were able to help Grove reduce air pressure and energy consumption by 50% in two main areas of their plant with the addition of air pressure regulators. We also helped them greatly reduce paint and solvent used in their finishing/cleaning processes by installing fluid pressure restrictors. Lower fluid pressures and optimal air atomization pressures contributed to an estimated 15-25% increase in paint transfer efficiencies, so a plural component proportioning system that previously sprayed 10 gallons of paint in one shift now only sprays 8 gallons. The increased paint transfer efficiency, faster flush times, lower VOCs produced, and reduced air compressor demand equaled substantial emissions reductions and a reduced landfill footprint. Lastly, the combination of these solutions greatly improved their finished product quality since paint rework due to overspray was drastically reduced.
Estimated Annual Savings
These solutions provided by C.H. Reed worked together, in tandem, to help increase energy efficiency, reduce waste, reduce their environmental footprint, and improve finished product quality. In the end, Grove expects to see an estimated annual savings of $159,600 based on their 2020 paint spend.
If you have compressed air and/or a painting finishing operation in your manufacturing plant and reside in the mid-Atlantic region, contact C.H. Reed to discuss your goals. We just might be able to help you save thousands in energy costs and material waste too!
Search
Categories
Get a consultation
Related Posts
The 3 Distinct Advantages of Hydraulic Powered Pumps
Recently, C. H. Reed helped a major printing operation install a new ink pumping system. The new system needed to transfer four colors of high viscosity, heat-set ink to their three presses, drawing the ink from multiple 5,000…
Simple Ways to Reduce Waste in Your Spray Finishing System
In today’s demanding manufacturing landscape, it can be convenient to adopt a “cut-costs-at-all-costs” mentality, justifying questionable means for the sake of leaner production, a lower bottom line and increased profitability. Regrettably, those efforts can interfere…
What You Need to Know About Air-Powered Pressure Washers
Pressure washers are great solutions for your average cleaning applications, but what tool do you turn to for your more challenging applications? There are many instances where it is simply impossible to use a traditional…