Contact our team of experts today!
"*" indicates required fields
Air Compressor Preventive Maintenance Programs
Just like any piece of mechanical equipment, all air compressor systems require some form of routine maintenance to ensure continuous, efficient and dependable performance.
Air compressor preventive maintenance programs are designed to identify problems in your compressed air system before they lead to expensive emergency repairs. These services increase an air compressor’s reliability and mean you won't need to take a reactive approach with repairs.
With C.H. Reed, you get to work with a service technician who can do everything from finding small cracks in belts to recognizing abnormalities with system performance. Partnering with our team for preventive maintenance programs for air compressors is the right move for avoiding downtime and revenue losses.
Why Preventive Maintenance Programs for Air Compressors Are Essential
Choosing the right team for preventive maintenance enables you to use air compressors in your facility with confidence. Over time, components such as belts, filters and valves wear out from repeated use.
Having a trained professional visit your facility for preventive maintenance work lets you prioritize employee safety, system performance and production outputs. Our technicians evaluate the effectiveness of electrical connections, intakes and related parts so you can continue operations without disruptions.
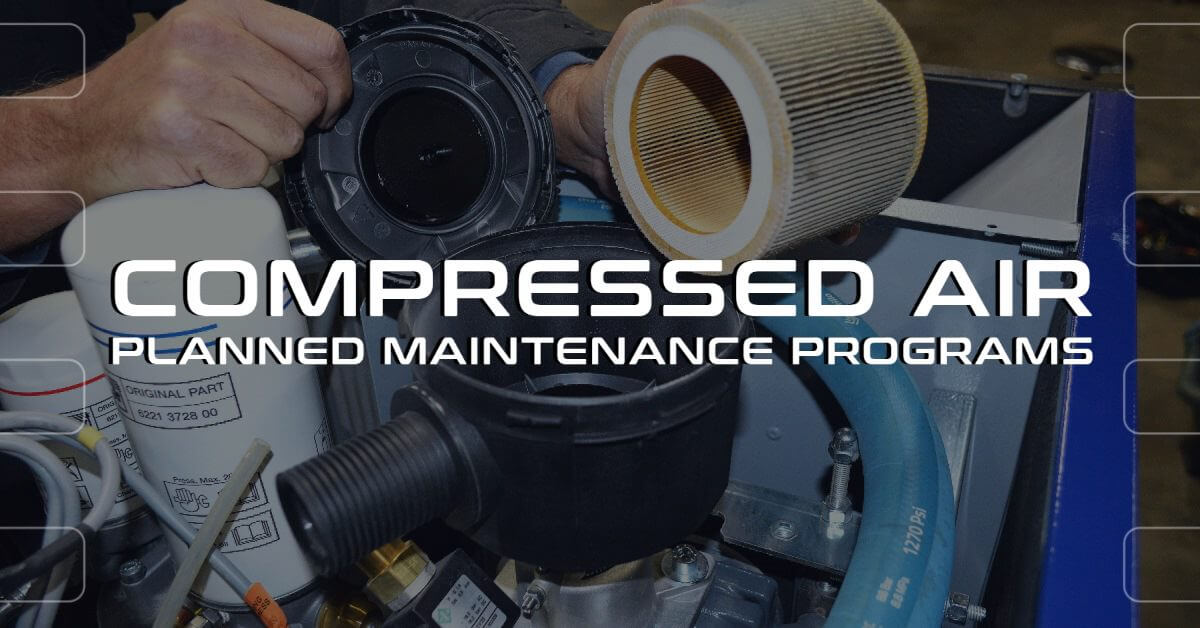
Advantages of Preventive Maintenance Programs for Air Compressors
No matter how small or large your compressed air equipment is, it is vital to perform preventive, planned maintenance services on a routine basis. Implementing a preventive maintenance schedule for your compressed air system yields multiple benefits.
Minimized Downtime and Operational Disruptions
For many manufacturers around the world, equipment breakdowns are the largest source of lost production time.
Along with lost production, downtime can result in loss of customer trust and business. When a company fails to complete preventive maintenance, it runs the risk of encountering air compressor performance issues with greater frequency. To minimize the risk of downtime, you need to perform planned maintenance without skipping a date, even when your air compressor appears to be running fine.
Fewer Emergency Repairs
If and when your compressor breaks down, you will need to get it up and running as quickly as possible. Not only can downtime cost you thousands of dollars in lost productivity, but it can also cost you thousands of dollars in unexpected repairs — something your organization may not have budgeted for. When compressor inspections and maintenance are performed on a set schedule, it allows you to identify issues before they get a chance to happen.
Lowers Energy Costs
Preventive maintenance allows you to identify issues before they over-exert your system. This allows your air compressor to run smoother and more efficiently — translating to less electricity used to power the equipment.
One horsepower of compressed air requires approximately eight horsepower of electricity. By increasing your system's efficiency through proper and routine maintenance, you'll enjoy significant energy savings for a healthier bottom line. Preventive maintenance plays a direct role in lowering your monthly electric bill.
Improved System Reliability
A huge benefit of preventive maintenance is that it increases the life and reliability of your entire system, not just your air compressor. When you calculate the upfront costs of a complete compressed air system, you want to ensure that you see a return on that investment through productivity. Without regular inspections, checkups and tuneups, your system’s reliability and efficiency decrease, lessening the returns you otherwise could have achieved.
Decreases Total Cost of Ownership
Most of the costs involved in generating compressed air for your plant are in the energy it takes to operate the equipment. A general rule of thumb when calculating the true life cycle cost of a compressed air system is that you will spend 12% on the initial purchase price, 12% on system maintenance and 76% on electricity to power the system.
Preventive Maintenance Provides Peace of Mind
Preventive maintenance programs provide you peace of mind knowing that your compressed air system is being properly cared for and monitored. You can breathe easy knowing that your system is running smoothly, minimizing interruptions and saving you money in the long run.
Meet Industry Compliance Standards
Having a professional complete compressed air system preventive maintenance in your facility makes it easier to abide by safety and environmental standards. Organizations such as the Occupational Safety and Health Administration (OSHA) and the Environmental Protection Agency (EPA) play a critical role in stopping unwanted accidents inside and around facilities nationwide.
Scheduling industrial air compressor maintenance is an excellent way to keep your business in good standing with compliance regulations that could otherwise damage your reputation when ignored.
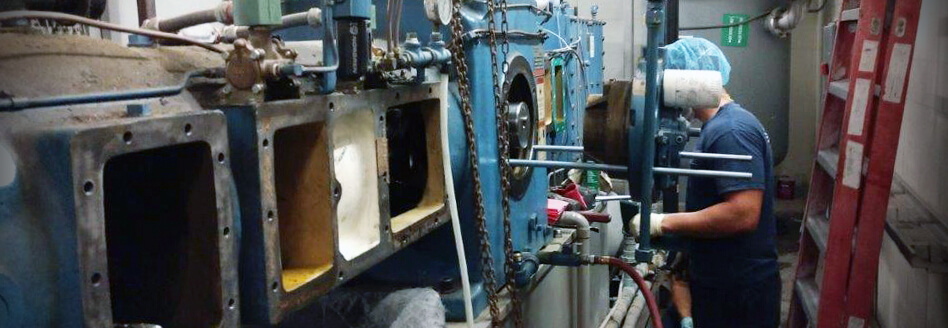
Compressed Air Service Consultations and What to Expect
If you have questions or concerns about your compressed air system and what type of preventive maintenance program you should consider, choose us and get a Compressed Air Service Consultant to help guide you. We will work with you to understand your specific business needs and give advice concerning industry best practices for compressed air system maintenance.
We're proud to assist manufacturers and industrial businesses in finding new ways to boost efficiency and sustainability practices through air compressor equipment. Our goal is to help you enhance product quality, employee productivity and your compressed air system configuration.
Our technicians serve you using a full-scale approach to air compressor maintenance:
- Performance assessment: Technicians review how your air compressor system functions in terms of energy usage and output. An evaluation of air compressor system components is done to gauge wear and tear.
- Maintenance plan development: Our experts consider the factors surrounding your air compressors to come up with a tailored maintenance approach. We will visit at a time that does not cause unnecessary downtime.
- Future scheduling: We help you decide on maintenance intervals so your air compressor system works as intended by the manufacturer for as long as possible.
- User training: Allow C.H. Reed to explain normal operating behaviors and when to seek help should something out of the ordinary occur between maintenance visits.
About Customized Planned Maintenance Programs from C.H. Reed
C.H. Reed helps you achieve optimal compressed air system performance with a customized planned maintenance program specific to your business’s particular needs. Our in-house and factory-trained, certified service technicians combine insightful industry knowledge and practical hands-on experience to ensure your compressed air system delivers reliable, efficient and quality compressed air to your plant.
We are proficient in working on all brands, models, sizes and types of compressed air systems. We help you meet your facility’s compressed air goals, serving these areas:
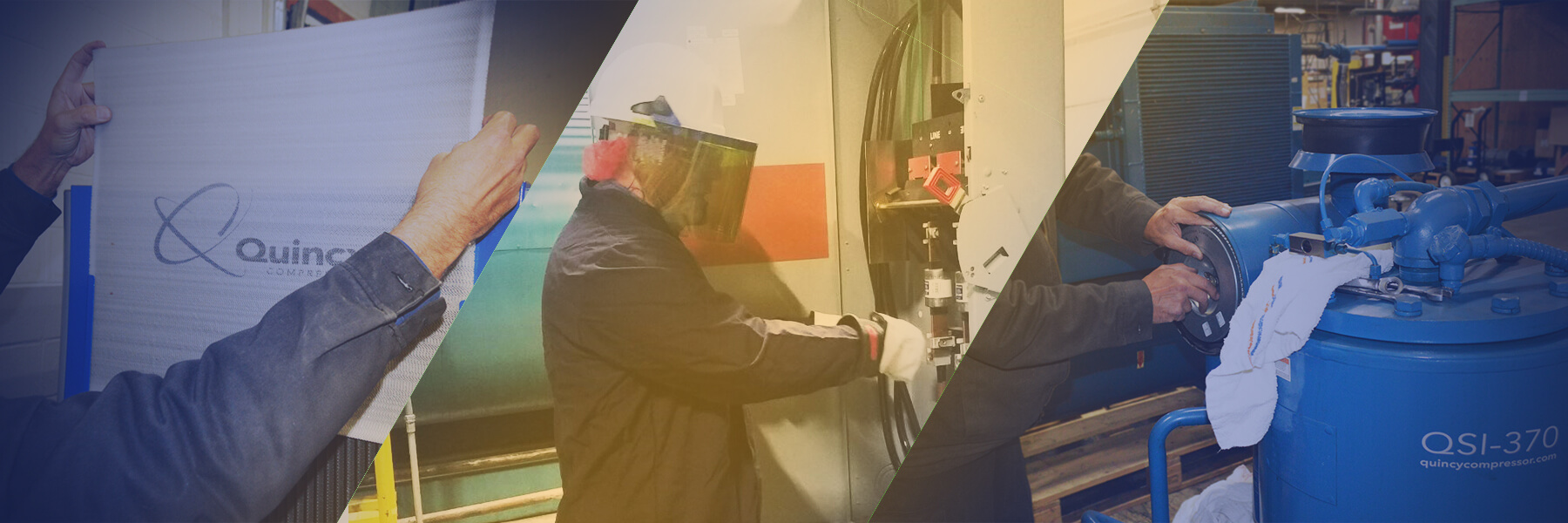
Get Started by Requesting a Quote Today
Eliminate guesswork when you contact us to learn more about preventive maintenance programs.
Before we provide a quote, we set up a site visit to gather all the necessary information surrounding your air compressor system. Below is some of the information that we need to collect in order to put together a price quote for you.
Contact our team of experts today!
"*" indicates required fields